Let us help you improve!
Our experts will help you optimize your workshop to the best it can be - call us and we will book a meeting!
Want a optimized workshop?
Fast and advanced equipment, effective and easy to use. And equipment that doesn’t go down when you need it most
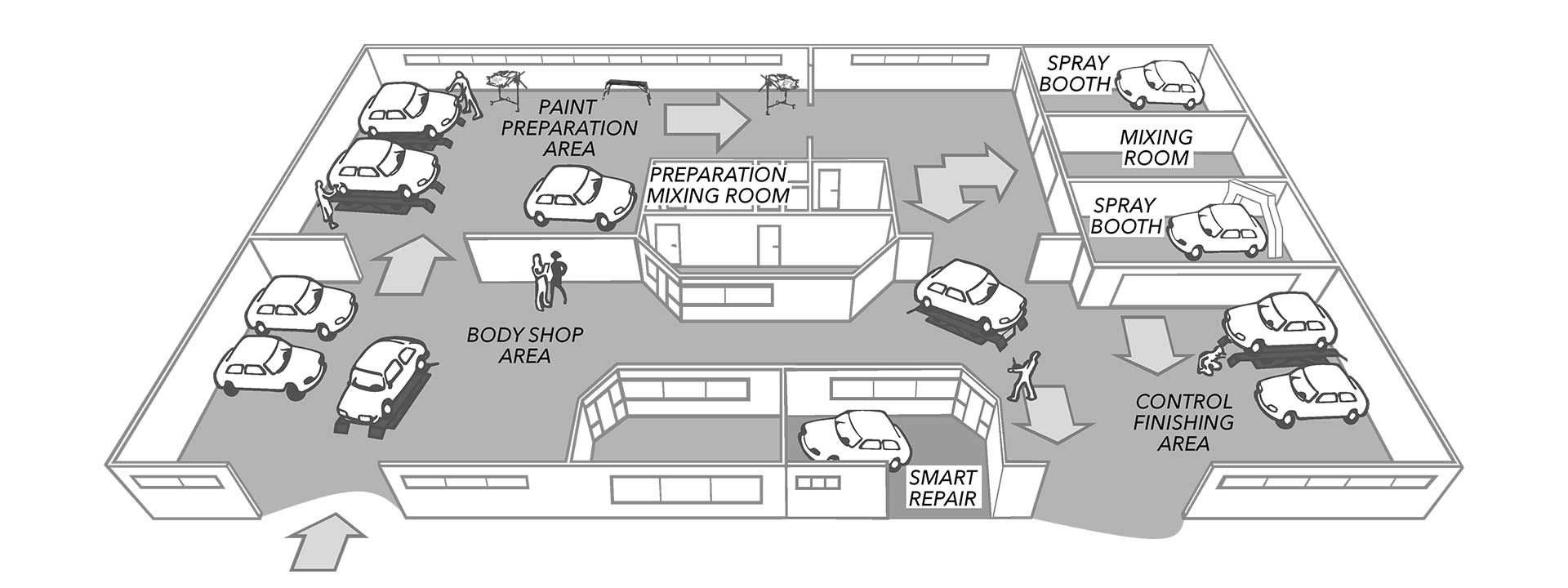
Panel Beaters
This is the first stop in a Body Shop, where the vehicle is deconstructed and panels are corrected. A first layer of putty is applied and sanded down. Hedson will solve problems as:
- Rapid throughput – by using technology to accelerate the work, preparing more cars quicker for the next phase.
- Safe vehicle transportation – The damaged vehicles need to be moved safely and efficiently, with minimal heavy manual maneuvering.
- High quality result – The first stop is the foundation for the result, doing it right here saves time and improves end quality.
Improve staff utilization – A Transmobile ensures a safer and quicker work routine that drastically reduces the work involved in vehicle transportation in the workshop.

Paint Preperation Area
This area is generally used for a variety of preparation processes like sanding, filling, taping etc. prior to painting.
Hedson will solve problems as:
- Maximize spray booth usage – generate an even flow during the day, optimizing the use of the spray booth.
- Safe and silicon free vehicle lifts – lifts need to be safe, but also exclude silicon. Silicon molecules can severely lower the end quality.
- Flexible solutions – essential for speeding up the workflow.
Ready to sand after 6 min – using an IRT infrared solution curing is done in 6 min. Saving time and improving throughput drastically.

Mixing Room
The Mixing room provides a work-space utilized to mix and prepare dusty/greasy liquids, like fillers and putty. Many of the liquids are solvent-based. Hedson will solve problems as:
- Space saving solutions – gun cleaners and other equipment must be compact for small mixing rooms.
- Excellent cleaning performance – a perfect gun cleaning result is essential for perfect painting result.
- A safe & cost effective system for solvents – a safe system for using solvents that reduces consumption, disposal and costs.
Up to 2x product lifespan – a Drester spray gun cleaner has a lifespan of 7-10 years while competing products has a lifespan of 1-3 years. In addition you adhere to the regulatory demands.

Spray booth
The purpose of the Spray area is to provide controlled environmental conditions while a vehicle is being spray painted.
Hedson will solve problems as:
- Optimize spray booth usage – optimized vehicle throughput requires fast and efficient vehicle transportation and curing.
- Accessories – by making it easier to reach the ceiling of an object that is to be spray painted, a step-bench can be used. Then the staff stands steadily and reaches properly.
- Clean spray guns – to insure a perfect result the spray guns need to be thoroughly cleaned.
Up to 3x quicker gun cleaning – to get a perfectly clean spray gun it takes approx. 8 minutes to clean by hand. With a Drester gun cleaner it is done in 2,5 minutes – whilst the personnel is able to do other tasks.

Drying area
This area is for curing paintwork after processes in the spray area. Short-wave Infrared (IR) and ultraviolet (UV)mobiles ensures deep penetration into the paint, as it cures from the inside out, unlike other heating methods that primarily cure the surface.
If solvents are “locked-in” in the paint layer, this can lead to destroyed paint work later on.
Hedson will solve problems as:
- Flexible solutions that saves energy – utilizing energy at the right place and with the right amount. Avoiding heating up the whole room.
- Flexible curing options – a rapid throughput of cars requires mobile/rail curing units with several programs.
- Safe curing method – vehicles include more and more electronics. Minimize harmful impact by using the right technology, ie IRT curing technology.Up to 89% time saving/ paint job, e.g.:
- Curing a wing or door, using a combined booth & owen at 60 degrees C = 40 min.
- Curing a wing or door, using IRT PowerCure = 7 min.
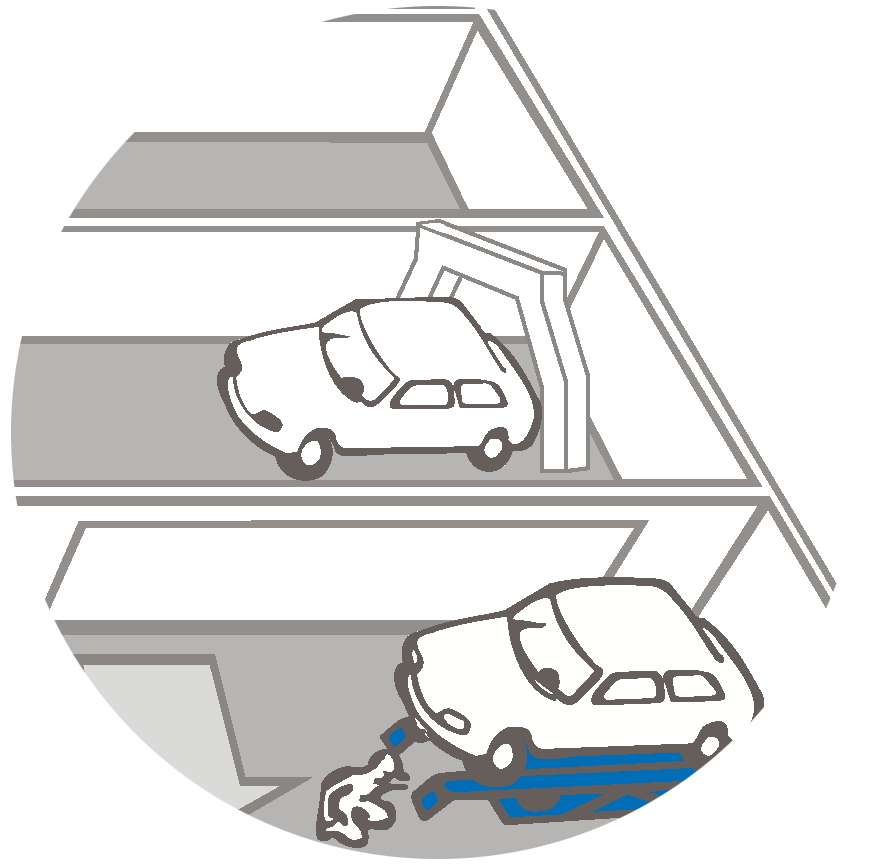
The finishing area is a holding area reserved for polishing and any necessary finishing processes. Customer needs are often similar to Preparation area 1.
Hedson will solve problems as:
- Efficient vehicle transportation – vehicle requires time-efficient vehicle transportation.
- Safe vehicle transportation – The cured vehicles need to be moved safely and efficiently, with minimal heavy manual maneuvering.
Improve staff utilization – A Transmobile ensures a safer and quicker work routine that drastically reduces the work involved in vehicle transportation in the workshop.

The finishing area is a holding area reserved for polishing and any necessary finishing processes. Customer needs are often similar to Preparation area 1.
Hedson will solve problems as:
- Efficient vehicle transportation – vehicle requires time-efficient vehicle transportation.
- Safe vehicle transportation – The cured vehicles need to be moved safely and efficiently, with minimal heavy manual maneuvering.
Improve staff utilization – A Transmobile ensures a safer and quicker work routine that drastically reduces the work involved in vehicle transportation in the workshop.

Smart repair – minor damages area
A area like this is used for taking care of small damages. Normally it is outside of the normal process of a body and paint shop and a job should be able to be finished in around 30 minutes
- Cost and time efficient – it will not reach the same result as a full process, but is a more cost and time efficient solution.
- Safe working environment – a lift is a great option for better working environment, health and quality of job
- Flexible and space saving – an mobile IRT dryer, provides flexibility and are easy to move around.
Reduce curing time – for minor jobs, a perfect choice to use is a mobile unit as an IRT 4-1 PcAuto or IRT Combi 4-2 IR/UVA.

Minimize downtime
Efficiency is the key to high profitability
A solution that works day in and day out, to minimize the downtime, is essential. The challenge is to optimize the workflow within and between the typical areas of Body- & Pain Shops. Hedson will solve problems such as:
- Efficient vehicle transportation
- Safe vehicle throughput
- Space saving solutions
- Boost productivity and throughput speed
- Minimize or eliminate bottlenecks
- Reduce waiting times
- Make the best possible use of floor space
- Improve end result, while also delivering health, safety and environment-related improvements
Areas described in this example of Body & Paint Shops are intended to provide a general framework as a guide to optimization. Click through the pictures to get more information about each area such as preparation area, mixing room and drying area.
Want a customized solution?
Need help with improving your efficiency? Do you want to know what problems we can help solving? Want a customized solution?
With the knowledge and experience within Hedson we will help optimize and improve the efficiency in your workshop.
Hedson experts will quickly analyse, plan and visualize the optimal and wanted result in your workshop.
We will help finding the best solution for your shop!
Book a meeting and lets see how we can improve your workflow!